Key Takeaways
- Waterjet cutting is a versatile technology used across multiple industries.
- It offers precision cutting without heat-affected zones.
- Applications include aerospace, automotive, and medical fields.
- Environmental benefits are notable in reducing waste and chemical usage.
- Technological advancements are continually expanding its capabilities.
Introduction to Waterjet Cutting
Waterjet cutting is a cutting-edge technology that uses a high-pressure stream of water, sometimes mixed with abrasive particles, to slice through various materials. Unlike traditional cutting methods, it does not generate heat, making it ideal for applications requiring precision without thermal damage. This method allows for clean, precise cuts, regardless of the material’s thickness or complexity. Manufacturers seeking a waterjet cutter for sale often look for versatile machines that meet these demanding requirements, accommodating various materials from metals to composites. Let’s dive into the numerous industry applications of waterjet cutting and explore how this technology transforms different fields.
Aerospace Industry Applications
The aerospace industry demands materials that are resilient and can withstand extreme conditions. Waterjet cutting is used to manufacture complex components from titanium and other robust materials, ensuring high precision and minimal material waste. The importance of accuracy in aerospace cannot be overstated, as even minor deviations can lead to significant flaws. Waterjet technology allows for the precise cutting of high-strength materials used to construct aircraft frames, turbines, and engine components. Additionally, the absence of heat-affected zones ensures structural integrity, a critical factor in aerospace engineering. This non-traditional cutting method has significantly reduced production time and increased efficiency, helping the aerospace industry to innovate and succeed.
Automotive Industry Innovations
In the automotive industry, waterjet cutting is utilized to create intricate parts and prototypes. This technology enables the production of smooth, burr-free edges, which are crucial for vehicle safety and performance. Car manufacturers benefit from the flexible and efficient nature of waterjet cutting for both small and large-scale production. Waterjet’s ability to cut various materials, including steel, aluminum, and carbon fiber, makes it invaluable for making everything from brake components to custom designs. Its precision reduces the need for subsequent machining, reducing costs and time. By adopting waterjet technology, automotive manufacturers can streamline operations, produce high-quality parts faster, and maintain stringent industry standards.
Medical Sector Utilization
The medical sector requires materials free from contamination and heat alteration. Waterjet cutting meets these standards, making it ideal for producing surgical instruments and implants. Its ability to accurately cut sterile materials ensures that the medical devices meet stringent health and safety regulations. Instruments like scalpels, scissors, and intricate implants benefit from the high precision that waterjet cutting offers. Additionally, this technology is used to manufacture diagnostic equipment and prosthetics, where precision and material integrity are crucial. The ability to cut complex shapes without compromising material properties has propelled waterjet cutting to the forefront of medical manufacturing, ensuring that products meet the highest standards of safety and effectiveness.
Environmental Benefits
Waterjet cutting also shines in its environmental benefits. Unlike traditional cutting methods, it does not produce hazardous fumes or excessive waste. According to an EPA report, waterjet cutting helps reduce the overall environmental footprint of manufacturing processes by eliminating the need for harmful chemicals and reducing the amount of waste material. This makes waterjet cutting an environmentally friendly option as it recycles the water used in the process and generates minimal material waste. Companies utilizing waterjet technology can comply more easily with environmental regulations and contribute to sustainable manufacturing practices. The reduced environmental impact makes this method particularly attractive in an age where eco-friendly solutions are increasingly sought after by industries and consumers alike.
Technological Advancements
Technological advancements have only increased the capabilities and efficiency of waterjet cutting. With innovations in precision and control, modern waterjet systems can cut intricate designs with remarkable accuracy. Continuous improvements ensure that waterjet cutting remains at the forefront of manufacturing technology. Enhanced software and automation have made these systems more user-friendly and reliable. Features such as automated nozzles, multi-axis cutting, and monitoring systems have expanded the range of applications, making executing more complex and precise tasks possible. These advancements also contribute to higher productivity, reduced operational costs, and better quality control. Staying abreast of the latest technologies ensures that industries can leverage waterjet cutting to its fullest potential, meeting ever-evolving market demands.
Real-Life Examples
Consider a scenario where a manufacturer needed to cut a highly durable material like carbon fiber for a high-performance racing bike. Traditional methods failed to cut it accurately without causing damage. By utilizing waterjet cutting, they achieved precise, clean cuts, significantly enhancing the quality of the final product. This ensures a better finish, structural integrity, and improved bike performance, illustrating the versatility and effectiveness of waterjet technology. Similarly, in custom art installations, waterjet cutting is used to create unique designs from metal and glass without any thermal distortion, allowing artists to realize their visions precisely. These examples underscore the adaptability and broad utility of waterjet cutting across various applications, highlighting its importance in modern manufacturing.
Conclusion
Waterjet cutting’s unmatched precision and adaptability have changed several sectors. It has many growing applications in industries such as aerospace and medicine. Numerous opportunities arise when many materials may be worked with without heat degradation. We can expect this fantastic tool to be used in even more creative ways as technology develops. Waterjet cutting still has much to offer regarding productivity, cost savings, and environmental sustainability. Waterjet cutting is better for producers who want to meet industry standards and produce high-quality products when producing precise medical devices or complex aerospace components.
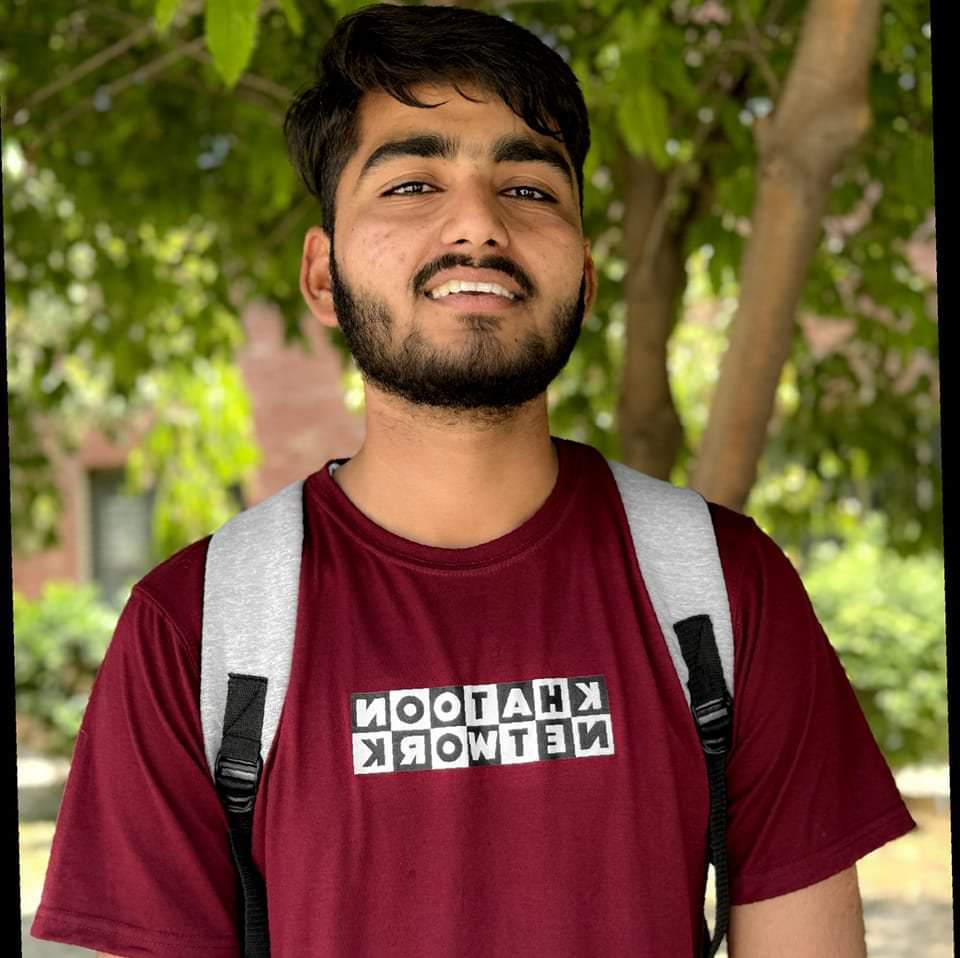
Asad Arshad, a prolific author of over 50+ websites across various niches, is open to collaboration opportunities. 🌐 For guest posts, reach out to him to benefit from his vast expertise and connect with a diverse audience. 📬